This week in the Imaging Lab, the Yale Peabody Museum is collaborating with the Near Eastern Languages and Civilizations department (NELC) to photograph Nubian artifacts for documentation purposes. NELC will be using Project Room 3 and the Hasselblad camera on the vacuum copystand to take high resolution photos of the artifacts. This equipment allows them to get highly detailed images that can be used for publication purposes. They will also be scanning old documents and maps related to this collection. Here is a little background on the project:
The Toskha Project
In 2008, the Yale Peabody Museum of Natural History in collaboration with the Yale Egyptological Institute in Egypt (NELC department) began a re-examination of the material from Nubian cemeteries of the so-called Simpson Collection.
In 1962, as part of the UNESCO Nubian salvage campaign, the Pennsylvania-Yale Expedition to Egypt excavated several archaeological sites in the area of Toshka. This expedition, directed by William K. Simpson professor of Egyptology, was a component of a larger campaign carried out between 1961 and 1963 that examined the region of Toshka and Arminna in Lower Nubia. Nubia is a region along the Nile river located in southern Egypt and northern Sudan. Several monographs resulted from this work, however, much of the archaeological material—particularly the Nubian Bronze Age cemeteries—remains unpublished.
The imaging project aims to produce a monograph with a systematic catalogue of graves and funerary offerings from Toshka West (TW) Cemeteries B, C, and D, the site of Gebel Agg at Toshka East (TE), and miscellaneous sites.
General information on burial ground and graves, including a sketch of shaft and inhumation, has been obtained from the original field notes, now housed at the West Campus Peabody Anthropology unit as part of the Simpson Archive. There are maps, photos and a few drawings from the original archive. The new high resolution photos of pottery vessels and jewelry, once part of the funerary offerings, are being taken to improve the quality of the documentation.
West Campus Peabody Anthropology unit: Roger Colten, Maureen White and Rebekah DeAngelo
Egyptology: Maria Gatto, Colleen Manassa and Alberto Urcia
Alberto Urcia is the digital surveying and virtual archaeology expert of the Yale Egyptological Institute and the person in charge of photographing the objects.

Nubian artifacts from the Anthropology division of the Yale Peabody Museum waiting to be photographed.
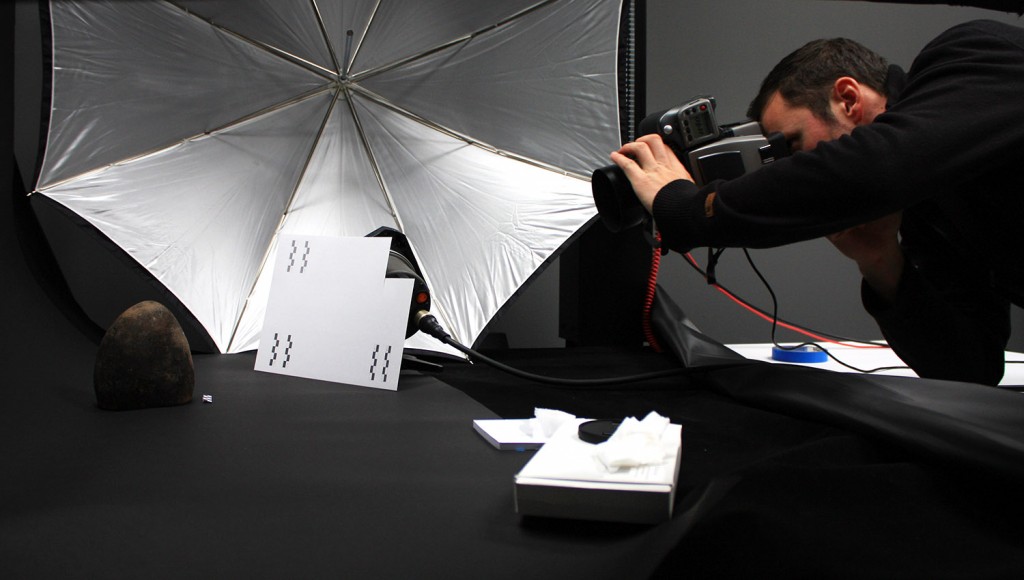
Alberto Urcia, Associate Research Scientist for Yale Egyptological Institute, manually adjusts the camera to make sure that certain areas of the artifact are in focus.

In an effort to remove shadows from the photograph, Alberto lights the artifact with an additional light source.

While normally used to shoot straight down, the camera on the vacuum copystand has been rotated 45 degrees to photograph the sides of all of the artifacts.

Alberto checks the clarity of the high resolution photograph. High resolution photographs allow researchers to view scratches, cracks and traces of paint at a high magnification.